Researchers from the Singapore University of Technology and Design (SUTD) have developed a technique for printing objects using cellulose, one of the main polymers occurring in wood.
They claim it will revolutionise manufacturing by providing a cheap, renewable and biodegradable alternative to plastic, creating conditions for a circular economy.
“We believe the results reported here represent a turning point for global manufacturing with broader impact on multiple areas ranging from material science, environmental engineering, automation and the economy,” said Assistant Professor Stylianos Dritsas, team joint leader.
“We are now at the stage of seeking industrial collaborators to bring this technology from the laboratory to the world.”
Cellulose offers a cheap and biodegradable alternative to plastic for printing objects, and the material produced can be further processed in the same way as wood, by drilling, sawing and sanding.
SUDT has succeeded in using the material to make a chair and a series of cellulose spheres. In other experiments, the team made a 1.2m-long turbine blade entirely out of its new material.
The goal of printing with cellulose is being pursued by a number of universities – for example, the Massachusetts Institute of Technology last year proposed using cellulose acetate, a derivative of cellulose used in cigarette filters, as a printing material.
However, SUDT claims, in a paper published in the scientific journal Nature, that it has found a superior low-cost, low-pollution solution that does not require any involvement with plastics.
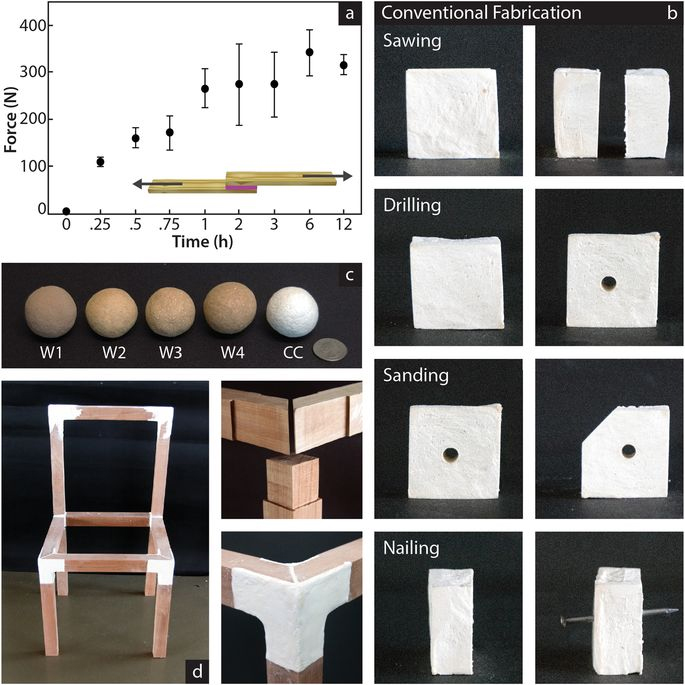
Objects made with the technique include this chair (SUTD)
The Singaporean method involved the introduction of small amounts of chitin between the fibres of cellulose. Chitin is kind of starch that forms the main component of insect exoskeletons and the cell walls of fungus.
The team found that chitin creates a strong, lightweight, inexpensive substance, which it calls a “fungus-like adhesive material”, or FLAM. Â
The team comments in their paper: “This material is completely ecologically sustainable as no organic solvents or synthetic plastics are used to make it. It is scalable and can be reproduced anywhere without specialised facilities. FLAM is also fully biodegradable in natural conditions and outside composting facilities.”
Javier Gomez Fernandez, team co-leader, said: “We believe this first large-scale additive manufacturing process with the most ubiquitous biological polymers on earth will be the catalyst for the transition to environmentally benign and circular manufacturing models, where materials are produced, used, and degraded in closed regional systems.
“This reproduction and manufacturing with the material composition found in the oomycete wall, namely unmodified cellulose, small amounts of chitosan – the second most abundant organic molecule on earth – and low concentrated acetic acid, is probably one of the most successful technological achievements in the field of bioinspired materials.”
According to the researchers, the cost of FLAM is in the range of commodity plastics and 10 times lower than the cost of common filaments for 3D printing, such as polylactic acid.
The researchers add that they have developed an additive manufacturing technique specific for the material.
Top image: The breakthrough was inspired by fungal spores (National Science Foundation)
Further reading:
Comments
Comments are closed.
Interesting development in the use of cellulose and chitosan as a sustainable, printable product but the article appears to claim wholesale manufacturing capability whereas the images appear to show only assembly/jointing capability. What’s what?
Steve, check the paper – they show the material being used for 3D printing there. The pics above are just castings.
Hey Steve,
If you look at the linked article, you can see some of the other projects the team has created with this fabrication method. The two videos are amazing.