A researcher in the US has developed a system of sensors and 3D modelling to monitor the structural integrity of scaffolding and other temporary structures in a bid to boost construction site safety.
Billed as a “Cyber-Physical System” (CPS), it alerts workers and managers by cell phone if structural parameters are violated.
Xiao Yuan, an architectural engineering PhD candidate at Penn State University, showed that the system can work in a lab, but it needs real-world testing before it can be used to address a persistent danger area in construction worldwide.
Her work investigated how putting sensors on the structures and linking them into virtual models can improve the safety of scaffolding, formwork and other temporary structures, upon which more than 75% of construction workers spend time.
It’s just like when we feel something if it hurts – the virtual model will feel if there is a problem– Xiao Yuan, architectural engineering PhD candidate
Improper construction and monitoring of temporary structures is a major safety concern. Of the top 10 most frequently cited OSHA standard violations in 2015 fiscal year, construction fall protection and scaffolding general construction requirements ranked first and third, respectively.
The system Xiao Yuan is developing would allow for remote monitoring of structures, and early warnings of potential failures to be sent to the cell phones of workers, safety inspectors and project managers.
“Once there is a problem, our virtual model will know,” Yuan said in an interview with the university press office. “It’s just like when we feel something if it hurts – the virtual model will feel if there is a problem.”
Automatic queries every two seconds monitor the structural integrity of the temporary structure based on predefined values. If no problem is found, the system just keeps collecting information.
If a potential failure is discovered, the hazardous section is highlighted in the 3D virtual model, indicating the need for further investigation.
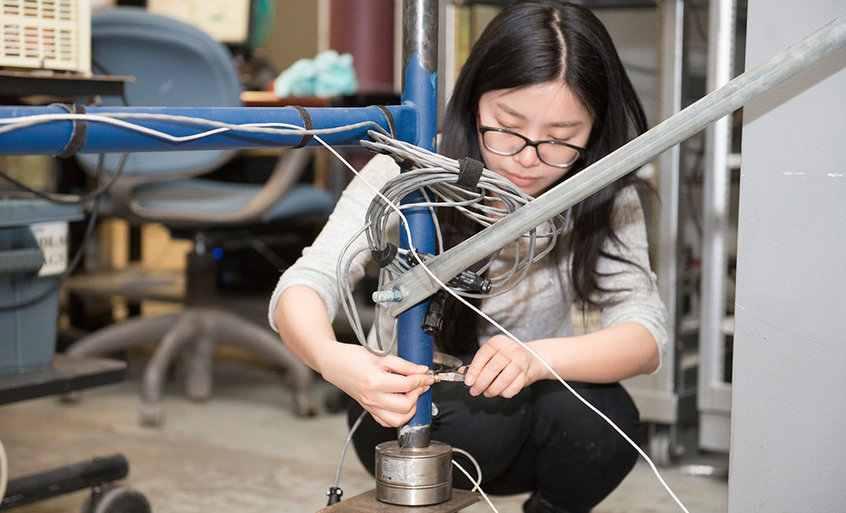
Xiao Yuan, architectural engineering Ph.D. candidate, connects and secures Cyber-Physical Systems (CPS) sensors on a temporary structure simulation (Penn State)
In Yuan’s research, various danger scenarios were simulated in labs, including: base settlement of scaffolding; overloading; severe displacement of scaffolding planks; the absence of a diagonal brace missing; lateral load by wind or being hit by a vehicle.
Yuan said the investigation is using machine learning technology to develop a self-learning model based on big data analysis. “The virtual model can learn from historical behaviour for intelligent identification of potential hazards in the future,” she said.
The system proved itself in the lab, but now it needs to be tested in the real world, Yuan said.
“There are some limitations to testing the system in the labs,” she said. “If we want to apply this technology in the real world, we need to test in the real world.”
Top image: Scaffolding at height in Germany (Frank Vincentz/Wikimedia Commons)