A young Indian entrepreneur and engineering student has been shortlisted for a global environmental award for his and colleagues’ efforts to commercialise a new kind of brick made from waste plastic.
The bricks are made by shredding plastic retrieved from bins or recycling centres, heating the shavings, and cooling the mixture in moulds.
Abhishek Banerjee, 22, a construction engineering student at Jadavpur University, has been shortlisted for this year’s Young Champions of the Earth Award, which is organised by the UN Environment Programme (UNEP).
The brick, called the “Plastiqube”, is intended to address two big problems in India.
One is that India produces over 25,000 tonnes of plastic waste every day, according to India’s Central Pollution Control Board, much of which ends up in landfills or finds its way into river and drainage systems.
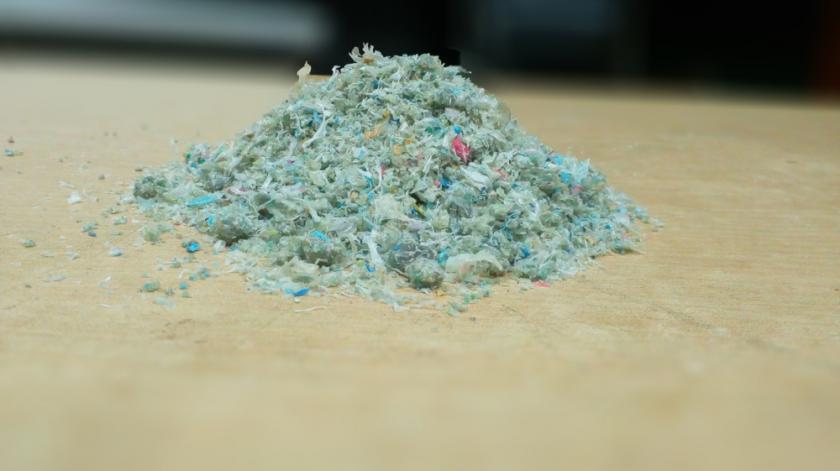
Plastic shavings used to make the Plastiqube. Photo by Qube
The other is that India’s conventional brick-making industry burns around up to 40 million tonnes of coal per year, pumping out carbon dioxide and sulfur.
Bannerjee says the Plastiqube needs 70% less energy than fired clay bricks.
The plastic brick is light, sturdy and has good thermal and sound insulation performance, according to Bannerjee’s social enterprise, Qube, formed in 2017 to commercialise the concept.Â
Co-founders of Qube are his engineering classmates, Agnimitra Sengupta, Ankan Podder and Utsav Bhattacharyya.
“I believe there should be a complete ban on single-use plastic materials by all the countries and the manufacturing of plastic should be regulated strictly,” Bannerjee told UNEP.
“However, most people tend to forget that there is still an awful lot of plastic in the oceans and spread across the land. Our options are either to work with this plastic waste or engineer new technologies for recycling it.”
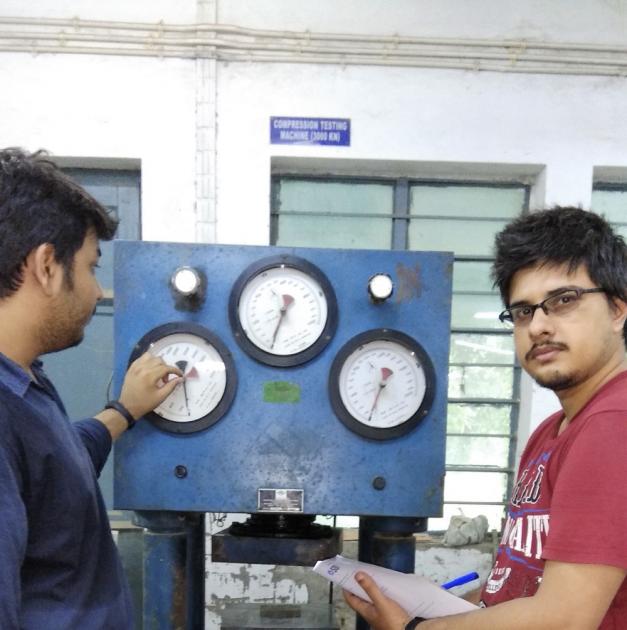
The Qube team at work. Photo by Qube
The Qube team works with waste collectors to gather plastic debris from dustbins and junkyards in the local area, after which the plastic is cleaned, shredded, heated and compressed into bricks.
The Plastqube faces several challenges. It’s fire resistance is lower than that of clay bricks, and they have not been accepted for large-scale construction.
“We are still developing our product to enhance the thermal resistance,” Bannerjee said.
Plastiqube is, however, supported and endorsed by Jadavpur University and India’s Ministry of Micro, Small and Medium Enterprise.
Top image: A plastic brick – the Plastiqube – made by the entrepreneurial team at Qube. Photo by Qube
Comments
Comments are closed.
What are the physical properties of your Plastiqube, i.e. compressive & tensile? What is the intended (cementitious) bonding material between your Plastiqube?
It would be a good idea to utilise plastic waste in the roads
Very good article sustainable until plastic completely banned