Disputes in construction are nothing new. In Greece, the Parthenon, and in the UK the more recent St Paul’s Cathedral were both blighted by delay. On the latter, Christopher Wren had his salary halved as a result.
In 1993, the Eurotunnel project saw cost overruns of over £1.2bn, leading to a series of disputes between those involved in its construction. The project costs are just a small part of the issue – time and money spent disputing can be equally debilitating for all involved. Â
In our modern, high-tech age are we any better at getting big things built on time, and to cost? The evidence suggests not.
In 2008, the CIOB’s study, Managing the Risk of Delayed Completion in 21st Century found that 31% of high-rise and 33% of power generation projects finish more than three months late.
Just 14% of projects use a fully linked network/schedule to manage time, and only 2% use an independent reviewer to check viability.
Of those interviewed, 47% felt the standard of training is sub-standard, and 57% feel there should be better education.
We looked at this century’s six most high-profile troubled projects and ranked them according to cost and time overruns. Can we learn from them?

Number 6: Wembley National Stadium, UK

Relatively modest cost overrun, but phenomenal legal bills (Source: Hill International)
- Commenced: 2002
- Planned Completion: Early 2006
- Opened: March 2007
- Delay: 1 year
- Planned Cost: £757m
- Final Cost (approx.): £1bn
- Increased cost: 32%
In 2007, the Wembley stadium project in the UK notoriously saw £1m spent on photocopying alone, during a lengthy and complicated dispute relating to issues including the roof design, the famous arch, and ground works.
By going to court and winning their claim, the contractor Multiplex lost £2m – a cost that ultimately was blamed for the sale of this previously successful 43-year-old company.
At first glance, this might not seem like too much of a failure – with a cost increase of just 32% (in part down to procurement route). But the cost in legal bills was phenomenal – Multiplex’s costs on a sub-trial alone (dealing with only a few of the issues at dispute) were quoted as being £45m.
UK newspaper The Telegraph commented in 2007: “The Wembley hangover has dogged Multiplex and seen the company struggling to restore its reputation just three years after it was listed in Australia.”
Number 5: Gorgon LNG Plant, Western Australia

Chevron’s Gorgon liquefied natural gas (LNG) plant is under construction on Barrow Island, 60km off the northwest coast of Western Australia (Source: Chevron)
- Commenced: 2009
- Planned Completion: 2014
- Completed: Ongoing – First production estimated late 2015
- Delay: Estimated 18 months
- Planned Cost: US$37bn
- Final Cost: Estimated US$54bn
- Increased Cost: 45%
Project trouble is no respecter of geography. Even 60km off the coast of Western Australia, with nothing but wildlife in the way (around 1,500 animals are reported to have been accidentally killed), megaprojects suffer delay and cost escalation.
The Gorgon project is set to deliver 15 million tonnes of liquefied natural gas (LNG) per year at its peak, and production is estimated to last until 2074. But, the project is currently at least a year behind schedule and is estimated already to be $17bn over budget.
Again, it’s known that there are disputes with hefty legal bills, but details are not made public. Gorgon’s remoteness may be part of the problem: last month workers negotiated more time for home leave and a 5% pay rise.
In 2014, Ernst & Young found that 64% of oil and gas projects face cost overruns, and 73% are behind schedule – an estimated increase in costs of US$500bn across 205 projects.
Number 4: Dubai Metro, UAE
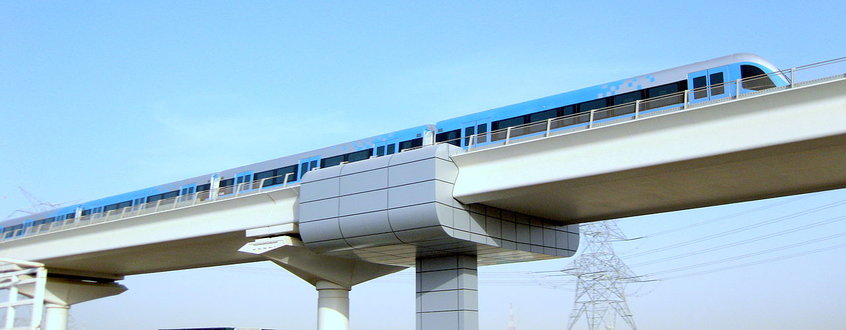
Panama chose the cheaper quote, but paid the price (Source: Hill International)
- Commenced: May 2005
- Planned Completion: September 2009
- Completed: March 2014 (final stations – line opened Sep 09)
- Delay: 5 years
- Planned Cost: $4.2bn
- Final Cost (approx.) $7.8bn
- Increased cost: 85%
The Dubai Metro was subject to a raft of disputes. Several billion dollars were rumoured to be at stake in the various arguments arising out of the light rail project designed to relieve some of the congestion in the rapidly expanding emirate.
Many disputes, particularly those dealing with international projects, are not settled in a public forum, which makes it difficult to be certain exactly how much is spent on their resolution.Â
Number 3: Olkiluoto 3 Nuclear Power Plant, Finland

A train completes a trial run on the Dubai Metro in February 2009 (Producer/Wikimedia Commons)
- Commenced: 2005
- Planned Completion: 2010
- Completed: Expected 2018
- Delay: Possibly eight years
- Planned cost: €3bn
- Final Cost: Estimated over €8bn
- Increased Cost: 166%
The notorious third reactor at Olkiluoto is still to be complete and has been dogged by delays, defects and disputes between the client, Finnish nuclear utility TVO, and the Areva-Siemens consortium responsible for building it.
Again we can’t know all the ins and outs, but as a sign of how wrong the project has gone, in August this year TVO upped the amount it is claiming from the contractor to €2.6bn.
Areva-Siemens, meanwhile is counter claiming for €3.4bn, making this project a contender for Mother of All Construction Disputes.
The same contractor is also overseeing a project at Flammanville in France, where the planned completion of 2012 has been put back to 2017 or even 2018.
Number 2: The Big Dig, Boston, USA

Construction on Boston’s ‘Big Dig’ still underway in August 1998 (David L Ryan/The Boston Globe via Getty Images)
- Commenced: 1991
- Planned Completion: 1998
- Opened: 2004 (95% complete)
- Delay: 6 Years
- Planned cost: US$2.8bn
- Final Cost: US$22bn
- % Increased cost: 685%
The ‘Big Dig’, or Central Artery Tunnel Project, in Boston, MA was a megaproject with mega problems. The goal was to move the ugly and traffic-clogged Interstate 93 expressway, which cut through the heart of downtown Boston, underground. The vastly complex project became known as the most expensive highway job the US.
Costed initially at $2.8bn (in 1982 dollar values), it was supposed to be finished in 1998, but only in 2004 was it 95% complete, and the final ramp began carrying vehicles in January 2006.
By then, construction costs had reached $15bn, inflated by interest to $22bn, according to The Boston Globe, which estimated that it would take until at least 2038 for drivers and taxpayers to pay for the scheme.
Among the numerous problems to beset the Big Dig were design flaws, use of incorrect materials, arrests for corruption and the tragic death of a car passenger caused by falling concrete ceiling panels in one of the tunnels in July 2006.
As with so many projects of this kind, the very ground itself proved a formidable foe. Relocating utilities, dealing with contamination, and preserving existing structures above ground were all cited as significant issues. Dealing with issues under the earth – particularly on such an elaborate network of tunnels, combined with a multitude of interfaces and contractors, seems to have led to one of the most spectacular delays and budget over-runs of America’s recent history.
Number 1: Scottish Parliament, Edinburgh, Scotland

- Commenced: 1999
- Planned Completion: 2001
- Opened: 2004
- Delay: 3 Years
- Planned cost: £50m
- Final Cost: £414m
- % Increased cost: 730%
While the numbers are smaller, the scale of the cost escalation makes the Enric Miralles-designed Scottish Parliament possibly one of the most spectacular failures of the century.
It was estimated that a fully fitted general hospital could have been funded by the resulting additional costs, not to mention the money spent on legal fees and disputes.
The primary cause of the problems appears to have been ‘scope creep’ – namely, changes to the size, scale and specification of the building while it was being built.
A public inquiry highlighted a number of issues: the use of a fast-track Construction Management procurement route was criticised, and ‘administrative oversights’ were quoted in the process. There was also concern over a lack of communication between parties to the contract.
So what can be done?
We estimate that more than £100m is spent every year in the UK on construction adjudication alone.
On top of that you would need to add in other, more expensive methods of dispute resolution – a large construction arbitration or court dispute may reach tens of millions of pounds.
Disputes continue despite new technologies such as BIM and the increasing use of technology and pre-fabrication in construction. What is the solution?
There are many factors involved in reducing the cost of disputes. Education in the following areas is critical:
- Contracts: Failure to properly administer a contract is cited as the number one cause of disputes. Understanding and managing the contract is critical. The contract will include ‘conditions precedent to entitlement’ and ‘notices clauses’ which must be carefully controlled. Whether NEC3, FIDIC or a local or bespoke contract, each will contain different provisions. The risks of modifying them, and their interaction with the local law will vary significantly.
- Records: The mantra over the past 15 years has been “Records, Records, Records”. It is critical to have good, ordered and ideally, electronic records. Such order helps to identify liability, mitigation and culpability in the event of a dispute – and contribute to managing the project as it progresses. The better the records, the more likely costs in a dispute can be minimised.
- Technology: Harnessing the latest technological developments will be key to disputes in the future. The use of tools such as BIM, computer aided graphics and other techniques can help ensure all parties understand your explanation.
- Approach: There are many routes to resolving a dispute and many requirements for dispute resolution in different forums, different countries and jurisdictions. The privacy of so many systems means that it’s essential to learn from those involved in the process how they work.
• Originally published 5 October 2015. Article amended 29 October 2015 to replace the Panama Canal project with Boston’s ‘Big Dig’.
• Stuart Wilks is a director at Hill International. These issues are discussed at Masterclasses organised by Hill International and the CIOB. More information is at www.hillintluk.com
Comments
Comments are closed.
ducation is essential throughout our Construction Industry! However it is at least equally ,if not more essential for the client to be fully educated in all the specifics relevant to the project and its satisfactory completion! Without such an education essential to a thorough understanding of just how its all been planned and just how all the risk factors have to be reduced and resolved via the continuous close collaboration of all the parties involved in the progress of the work! Via regular collaborative purposeful deliberation , consensus on the way forward has to be decided on and strictly followed through! I say that by making the client an integral and essential part of the management structure mutual understanding is engendered and misunderstandings are eliminated! It should go without the saying that all our appointed professionals including municipal building inspectors be part of the management structure as well! Consensus is signed for by each and all, each and every time and fully taken on record and securely filed for future reference! Q.E.D. !!
Good piece though obviously oversimplified to fit word length. For a (slightly) more in depth analysis and a different angle on “why” and “what to do about it” check out my book “We need to talk about collaboration”. It’s a free download from my website and takes about 2 hours to read.
regards
Dave Stitt
A very well written article. I was surprised to know that Dubai Metro had such a huge over run. And this in spite of hiring the best consultants and contractors.
Och aye the noo, that’s got ta hurt.
While I accept that this is a simplified summary, it paints a somewhat gloomier picture than reality would suggest, especially as regards:
The Scottish Parliament, for which a figure of £50m was never realistic: it was based on the figure used as the basis for the design competition, which was just pulled from the air. Most of the scope creep arose from MSPs seeking expansion to their individual fiefdoms on a piecemeal basis, which is why their subsequent shrieking was less than convincing and the vilification of RMJM so disgusting.
Dubai Metro, which opened a large number of its mainline stations on 9/9/09, as anticipated, and from that date on provided a workable metro solution for a great deal of the city. The vast majority of both lines was fully workable by 10/10/10. As far as most people are concerned, it pretty much opened on time, despite a funding crisis caused by the financial collapse with a year to go.
I think in most cases, the secret is the Owner not just hiring the best PMC’s,Contractors etc. but a clear definition of the Owner/PMC relationship from the beginning,effective project governance and creation of the right structure inside Owner’s organization to effectively monitor project’s progress and facilitate project decisions.
Thanks for the above comments – you’re quite right that the article was adjusted for space and some editorial changes made. For me, what’s particularly interesting is the table. Proportionally, the cost increase on these projects appears to far outweigh the time, indicating the huge cost of failing to plan and subsequently trying to get things back on track.
If anyone’s interested, my colleague Steve Briggs has written a useful paper on time management. Not sure the link will work here, but: http://bit.ly/WYZpyb
With the Scottish Parliament in particular, we did consider using an original estimate of £10m but felt that was unfair. However, you’re quite right about the source of the scope creep, most certainly down to the client. We of course haven’t even mentioned a certain tram scheme in the same city.
You have to ask yourself why the Scottish Parliament went so wrong?! Large complex projects are too big to allow 1 person to hold all the reigns, thereby making it crucial that each person involved takes full responsibility for their input, including making it know to all. I think taking full responsibility and communication are key. For example, it would appear the user group did not consult sufficiently, and/or the decisions on the building use/design were totally inadequate requiring changes through out the build – a contractors nightmare client for which they obviously charged dearly!
More surety before starting the build, and more care with public money is obviously called for!
Philippa
In every major project there is a reality that selecting the cheapest bid with an ill defined scope of supply will always result in an increase in cost and an extension to the contract time frame. If there is anything that I have learnt is you can reasonably expect the estimate cost to be double and take you four times as long or four times the cost and twice as long if you don’t understand the scope of supply or the complexity of the project. I know that this is very simply put but absolutely right in most large infrastructure projects.