By Dan Smith in Kumasi, Ghana
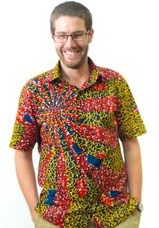
It must be incredibly difficult accurately to estimate the cost of large projects in Ghana, such as the Hope technology city near Accra, estimated to cost $10bn, or the Sky Train proposed here in Kumasi, costed at $170m.
Here, as in most developing countries, the market prices, inflation rates and exchange rates fluctuate wildly, making estimating an art more than a science.
I’ve been working in Uganda and Ghana for two years now. There are no standard prices for materials and, if you do get a price list, it’s probably only valid for a few months.
In a place where information is scarce you need to know who and where to buy from, a value from which to start haggling, and you need a buyer you can trust – unless you want the “obruni price” or to a pay a “muzungo tax” – the ironic terms bandied about to explain why traders inflate their prices at first sight of a foreigner.
When you move from town to town these people, places and prices will change. Then if you check back in a few months they could have nearly doubled.
In Uganda I was working with projects of less than a thousand pounds aimed at micro-enterprises and household investment through micro-finance. In Ghana I’m working on a cartridge processing site valued at around £25,000. It’s partly constructed by employing a contractor and partly through managing our own labour.
It’s nothing “mega”, like a technology city or a mass transit scheme, but it is exactly the sort of project undertaken everywhere by households and small to medium sized businesses here, the sort that accounts for the majority of construction activity, and the size that most people have to deal with.
When I arrived in Ghana in October last year, to work with Clean Team Toilets, I was given a bill of quantities from a previous design. That put the unit rate for pouring a cubic metre of concrete at 220 Ghana Cedis (US$83 at current exchange rates).
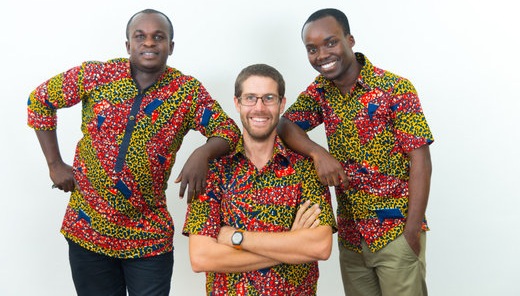
Engineer Dan Smith, middle, with Emmanuel Essandoh, left, Clean Team Ghana operations supervisor, and Kofi Yeboah, chief of communications, Clean Team Ghana (Sesinam Dagadu & Clean Team Ghana Ltd)
Having seen dramatic price fluctuations in Uganda I went to some excellent local engineers from the Building Roads and Research Institute – a National centre of excellence in the construction and transport sectors.
Their estimate in February put a cubic metre of concrete at 320-350 Ghana Cedis ($120-$130) – a 50% increase in less than six months.
Why such an increase? During this period inflation was generally at 13%-14% which has a cumulative effect on prices and alters how valuable Ghana’s currency is. People are also complaining that the basic cost of living has doubled in the past year which also affects how much a labourer will want for his time – although wages rarely increase at the same rate as inflation.
Then there is the issue of supply. Take laterite, the ubiquitous iron-rich gravelly clay material used for road construction across the continent. There is no central laterite supplier in Kumasi. So you have to order from the latest quarried area and, to guarantee quality, you have to inspect the material before making an order.
Only those ‘in the know’ can tell you where the latest quarry is being dug. If it happens to be close to your site it could be cheaper. But the quarries vary in size, so, if there’s a big project starting up in the vicinity, that quarry might have been emptied between you getting a price and placing an order. If the nearest quarry is not so near, you’ve got a sizeable haulage bill to haggle over.
The rate of inflation is remarkably unstable. In Uganda I worked with Engineers Without Borders UK and Water For People create the Sanihub project -Â a research project developing intermediate technologies for pit latrine emptying businesses.
While I was there inflation plummeted from 21% to 6.7% between July 2012 and January 2014, dipping, in-between, to a low of 3.6%. I believe it’s going up again now due to the recent anti-homosexuality legislation, which has led to a freeze on foreign financial assistance.
With that in mind an increase in the price of, for example, a corrugated iron sheet by 10% every few months seems quite reasonable.
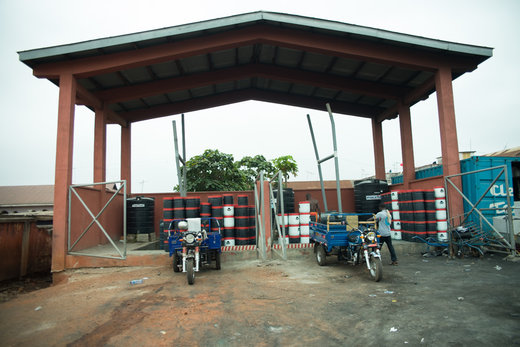
Processing site in Ashtown, Kumasi, where cartridges from Clean Team’s rental toilets are processed. The site was allocated by the Kumasi Municipal Authority but Clean Team is moving to larger premises, currently under construction, to expand operations
In Uganda the majority of industry is based around the capital, Kampala. Fuel is imported via Mombasa in neighbouring Kenya and crosses two borders, each with its own risks of bureaucratic delay and bribery. It took us nearly seven months to ship equipment from the UK to Kampala because of this.
This means that imported products are expensive, including fuel. The cost of fuel has a direct impact on the cost of transport from the factories to the rest of the country; prices normally increase with the distance and difficulty of hauling the goods there. But making an accurate correlation between distance and price differential is almost impossible.
Small and large projects alike are affected by this massive cost uncertainty and in major public works it must leave a lot of room for corruption.
Last month a four-year study by Oxford University researchers concluded that large dams throughout history have suffered average cost overruns of 96% and that the overrun increases exponentially with the size of the dam.
The underlying reasons are many and the situation is unlikely to improve much any time soon. Meanwhile people still need homes and schools and infrastructure. Not only are people profitably building these things in countries like Ghana, they’re some of the few economies showing any growth at the moment. So if you can understand the system, there’s money to be made.
• Dan Smith is a civil and environmental engineer working with Clean Team Toilets in Kumasi, Ghana. His next challenge is an MPhil in Engineering for Sustainable Development at the University of Cambridge, after which he hopes to use his experience to lead civil engineering projects in frontier markets