A team of researchers in the US has begun rethinking the design of wind turbine blades to achieve one that is more than twice as long as the biggest available now and that could give a single turbine a 50-MW capacity – more than seven times greater than today’s most powerful turbines.
The blade sought by Sandia National Laboratories and a number of universities would be 200m long – just short of the length of two American football fields – and would fold inward like a palm tree to protect itself in a hurricane.
Stiff blades are heavy, and their mass, which is directly related to cost, becomes even more problematic at the extreme scale due to gravity loads and other changes– Sandia National Laboratories
By using ultra-light, hollow segments, the scientists hope to revolutionise the design of turbine blades, the biggest of which today extend to around 80m (such as the one pictured above needing two vehicles to turn a corner) on turbines with a 7-MW generating capacity. Most current US wind turbines produce power in the 1-2 MW range, with blades about 50m long.
Funding for the research is provided by the US Department of Energy, and comes as developers have begun moving ahead with the country’s first major offshore wind farms.
“The US has great offshore wind energy potential, but offshore installations are expensive, so larger turbines are needed to capture that energy at an affordable cost,” said Todd Griffith, blade designer at Sandia, in an article describing the project.
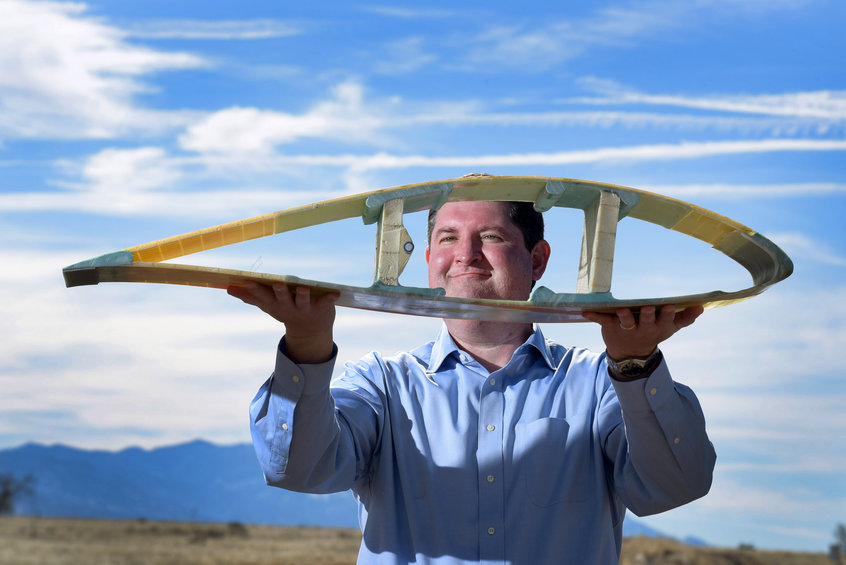
Blade designer Todd Griffith with a cross-section of a hollow blade segment that illustrates the principle behind a 200-m blade (Randy Montoya/Sandia National Laboratories)
The University of Virginia is leading the research, with Sandia, and scientists from the universities of Illinois and Colorado, plus the Colorado School of Mines and the National Renewable Energy Laboratory are also involved. Corporate advisory partners include General Electric, Siemens, Vestas and Dominion Resources.
Keeping palm in a storm
Sandia calls its concept of a gigantic bendy blade the “extreme-scale Segmented Ultralight Morphing Rotor”, or SUMR, and says the inspiration comes from the way palm trees behave in tropical storms.
Most turbines now face the wind, but the SUMR would face the other way. At dangerous wind speeds the blades would fold inwards to reduce wind loads and cut the risk of damage. They would spread back out when the wind slows to catch more of it.
Keeping the blades light and flexible overcomes a number of barriers to size, Sandia says.
“Conventional upwind blades are expensive to manufacture, deploy, and maintain beyond 10-15 MW,” Todd Griffith said. “They must be stiff to avoid fatigue and eliminate the risk of tower strikes in strong gusts.
“Those stiff blades are heavy, and their mass, which is directly related to cost, becomes even more problematic at the extreme scale due to gravity loads and other changes.”
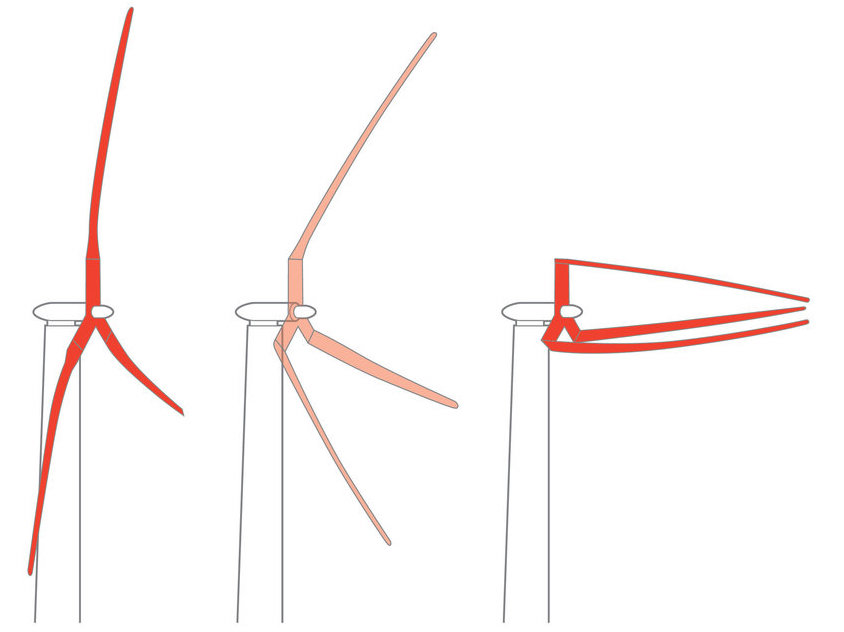
At dangerous wind speeds, the proposed blades fold to reduce wind loads. At lower wind speeds, the blades spread to maximise energy production (Sandia National Laboratories/TrevorJohnston.com/Popular Science)
According to Sandia, studies show that load alignment can dramatically reduce peak stresses and fatigue on the rotor blades.
By segmenting the blades they could be manufactured more cheaply and transported more easily, Griffith added.
Last year the US government confirmed its goal of wind power providing 20% of the nation’s energy by 2030.
Gigantic turbines could be an important way to meet that goal, said Sandia National Laboratories, which is operated by a subsidiary of Lockheed Martin and conducts research and development for the US Department of Energy.
Top photograph: An 83.5-m-long blade made by Denmark’s SSP Technology in transit to Scotland in 2013. It was called the longest blade in the world at the time (SSP Technology)
Comments
Comments are closed.
It reminds me of the axiom: ” give me a leaver long enough and I will move the world!” I wonder if they have ever thought of sectionalised sliding extendible and retractable wind turbine blades – extendible at lower wind speeds and retractable at increasingly higher wind speeds? This would enable the manufacture of a 200 meter fully extended long blade in a number of shorter sliding sections which slide into one another thus drastically reducing the transport problems and associated costs!! If they can do it with our road mobile crane jibs why not with wind turbine blades!?