Cement makers have long been criticised for being heavy industrial polluters, but now a consortium of international firms is building a new kind of plant in Belgium which they say could capture more than 95% of CO2 emissions from lime and cement manufacturing.
This new “direct separation” technology adds potentially no additional energy costs and can slash the environmental impact of an industry that is responsible for 5% of global carbon emissions, participants in the pilot claim.
Part-funded by the European Union (EU), the plant will be built at the HeidelbergCement site in Lixhe, Belgium once necessary permits have been secured, and will then undergo two years of extensive testing.
The project is being led by an industry grouping called the Low Emissions Intensity Lime and Cement consortium (LEILAC), which includes HeidelbergCement of Germany, Mexico’s Cemex, UK materials firm Tarmac and Calix, an Australian mineral-processing and carbon capture technology company.
LEILAC was set up to exploit carbon capture technology developed by Calix, which may enable Europe’s cement and lime industries to slash their carbon emissions without significantly increasing their costs.
The consortium says carbon capture will need to be applied to most European cement plants if the EU is to meet its 80% emissions reductions targets by 2050.
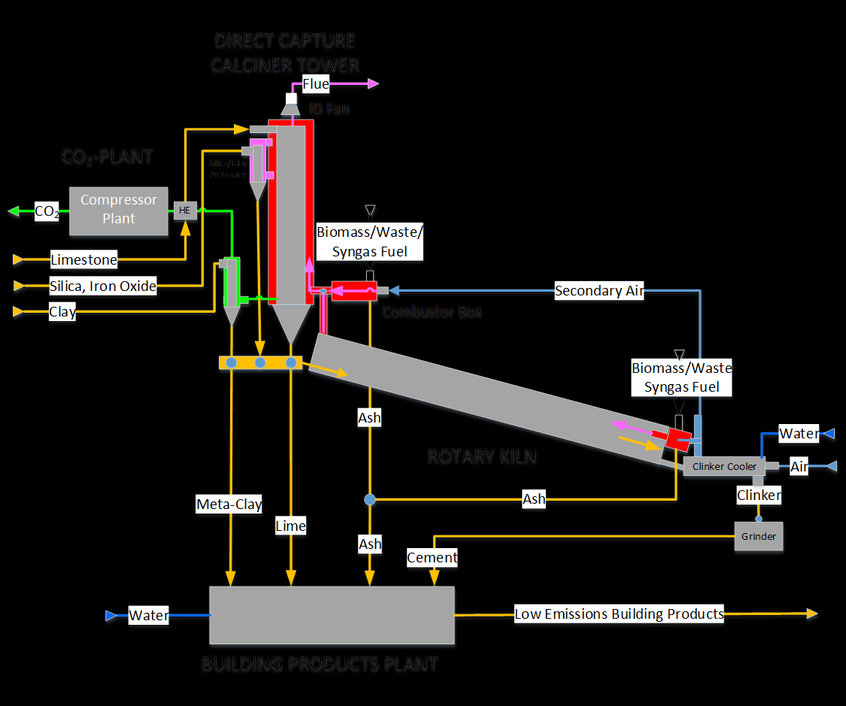
The process flow in Calix’s Direct Separation Calciner
This €21m ($24m) scheme will receive €12m ($13.5m) over five years from the EU’s Horizon 2020 research and innovation programme. The remainder will be provided by the consortium’s members.
Phil Hodgson, the chief executive of Calix, commented in the company’s newsletter: “Around 60% of the total carbon dioxide emissions from cement and lime plants are released directly, and unavoidably, from the chemical reaction in the production process.
“Calix’s ‘Direct Separation’ technology uses indirect heating in which the process carbon and furnace combustion gases do not mix. This re-engineering of the process flows enables the capture of almost pure carbon dioxide released from the limestone, without significant additional costs or increased energy use.”
The high-temperature Direct Separation Calciner pilot unit will undergo two years of testing at a feed rate capacity of 240 tonnes a day of cement raw meal and 200 tonnes a day of ground limestone, Calix said.
The process will be studied to see if the technology can be scaled up. The project results will be shared with industry at intervals during the testing.
Other members of LEILAC are Belgian limestone producer Lhoist, UK engineer Amec Foster Wheeler, the Energy Research Centre of the Netherlands, Imperial College London, Spain’s PSE Cement Trading, Swiss environmental consultant Quantis and the UK’s Carbon Trust.
If the pilot points to commercial success it could substantially cut emissions from cement production, which is growing by 2.5% annually.
Comments
Comments are closed.
This is the wrong solution. The release of carbon dioxide is a major cause of global warming, so instead of using a process that produces carbon dioxide use a different glue to stick materials together. Simple?
Instead of using heavy materials to construct buildings, use light materials that use less energy to move thus saving energy and releasing less carbon. Our love affair with bricks and mortar has to stop and be replaced by more sensible materials. We have been using concrete more and more since Roman times, but we don’t have to continue to make the same mistake. We could use the amazing advances in materials to transform our buildings. Bricks and concrete are porous and transmit heat so we compensate by damp proofing and insulating, but why not start again with damp proof and naturally insulating materials? The only answer is lack of imagination! So lets imagine a world without bricks and mortar rather than prop up this outdated technology.
I would partly agree with Matthew however concrete has many other attributes. This week BSI released a new publicly available specification for alkali-activated cementitious binder materials that offer ca 80+% saving compared to ordinary Portland cement production using recycled and industrial waste by products that use little or no energy to manufacture. This PAS8820:2016 should be used by all engineers interested in the future of construction with low carbon at its heart. So you can still have concrete just make it from waste for a fraction of the investment in plant!
The real answer is so very simple! Stop the huge ,insane wastage of all of our manufactured materials which result in mountains of useless polluting and unsightly discarded and mostly pre-retrievable and eminently RECYCLABLE AND THEREFORE REUSABLE( AND MUCH LESS COSTLY TO REPRODUCE THE FULL RANGE OF NEW FULLY FUNCTIONAL) MATERIALS AND PRODUCTS ( INCLUDING CONSTRUCTION) NOW IN DEMAND WORLDWIDE!!! Then once a system of voluntary and legally enforced recycling has been established – then we can continue with research into improving the functional properties of the full range of such re-manufactured materials according to the general public demands made on our industry! We cannot rely on ever diminishing raw materials being available forever!