24 July 2013
The chemical secrets of a concrete Roman breakwater that survived the last 2,000 years submerged in the Mediterranean have been uncovered by an international team of researchers at the University of California, Berkeley.
The study, part funded by Saudi Arabia’s King Abdullah University of Science and Technology (KAUST), has pinpointed why the best Roman concrete was so good when modern concrete often shows signs of degradation after just 50 years in sea water.
Researchers also discovered why making Roman concrete was somewhat less environmentally damaging.
Using the Advanced Light Source at Lawrence Berkeley National Laboratory (Berkeley Lab), a research team from UC Berkeley examined the fine-scale structure of Roman concrete, and discovered for the first time how the compound – calcium-aluminum-silicate-hydrate (C-A-S-H) – bound Roman concrete so well.
They calculated that making Roman concrete was also less energy intensive than our concrete.
Ours uses Portland cement, made through a process of burning limestone and clays at about 1,450 degrees Celsius – which is why seven percent of global carbon dioxide emissions every year comes from making Portland cement.
The lime in Roman concrete needed temperatures around two-thirds cooler, researchers say.
The study looked at samples of Roman concrete taken from a breakwater in Pozzuoli Bay, near Naples, Italy.
“Roman concrete has remained coherent and well-consolidated for 2,000 years in aggressive maritime environments,” said Marie Jackson, a UC Berkeley research engineer in civil and environmental engineering and lead author of two papers on the research.
“It is one of the most durable construction materials on the planet, and that was no accident. Shipping was the lifeline of political, economic and military stability for the Roman Empire, so constructing harbors that would last was critical.”
The recipe for Roman concrete was described around 30 B.C. by Marcus Vitruvius Pollio, an engineer for Octavian, later Emperor Augustus.
Pollio described how Roman’s used volcanic ash in their lime to form mortar. They packed this mortar and rock chunks into wooden molds immersed in seawater.
So, rather than battle the sea, Romans made it an integral part of the concrete.
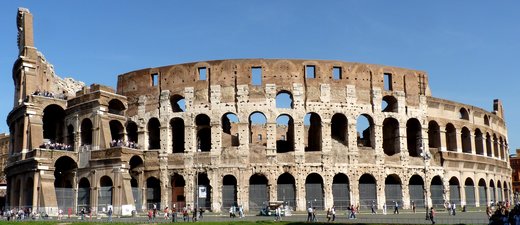
The Colosseum, Rome, built of concrete and stone (Dudva/Wikimedia Commons)
The researchers also identified a very rare hydrothermal mineral called aluminum tobermorite (Al-tobermorite) that formed in the concrete.
“Our study provided the first experimental determination of the mechanical properties of the mineral,” said Prof Jackson.
A wholesale re-adoption of the classical concrete recipe is unlikely, however, because Roman concrete took considerably longer to set.
But the researchers are now finding ways to apply their discoveries about Roman concrete to the development of more earth-friendly and durable modern concrete.
They are investigating whether volcanic ash could be a substitute for fly ash – waste from burning coal – which is used to produce a greener version of concrete today.
There is not enough fly ash in the world to replace even half of the Portland cement being used, but the search is on for alternative, local materials that will work, including the kind of volcanic ash that Romans used.
Researchers believe such alternatives could replace 40 percent of the world’s demand for Portland cement.
The research began with initial funding from King Abdullah University of Science and Technology in Saudi Arabia (KAUST), which launched a research partnership with UC Berkeley in 2008.
Researchers noted that Saudi Arabia has lots of volcanic ash that could potentially be used in concrete.
Source: UC Berkeley