27 September 2013
The UK has a new ‘industrial strategy’ for construction, and it involves trying to get a bigger slice of the global construction pie. But will it work? Rod Sweet reports
Some British designers, consultants and contractors enjoy big international reputations, but the fact is, UK construction is a stay-at-home industry.
According to government figures, construction services and products account for only 2% of all UK exports.
Leading the modest charge are contractors, whose work abroad led to a UK net trade surplus of £590m in 2011, the government says.
Close behind are architects and surveyors, thanks to whom UK Plc sold £530m more in design and consulting services than it bought in the same year.
But dwarfing these surplus slivers is the UK’s £6bn trade deficit in construction products.
According to 2013 figures the UK exported £6bn worth of products and materials, but imported twice that – £12bn worth.
With domestic construction output growth weak and stuttering – apart from a slight upturn hailed this month in private house building – the UK government believes something must be done to revive an industry that employs 10% of the UK workforce, and one that is clearly ailing.
This summer it launched a new “industrial strategy” for construction, called “Construction 2025”. (Access it here.)
Over the years many reports have tried to spur improvement in the industry (and bring down the cost of public sector projects) and this latest sets out three goals that echo previous missed targets: 1) a 33% reduction in the capital and the whole-life cost of built assets; 2) a 50% cut in build time, and 3) a 50% reduction greenhouse gas emissions.
But it contains a fourth, which is new: a 50% reduction in the UK’s construction trade gap.
Seizing the imagination of politicians is just how much construction is booming elsewhere in the world, while it stagnates at home.
World construction output will grow by more than 70% to $15 trillion by 2025, according to a July report by Global Construction Perspectives and Oxford Economics.
But China, India and the US will account for almost 60% of that growth.
And generally the action is in emerging markets where 52% of all construction activity is today, a proportion that will rise to 63% by 2025, the report says.
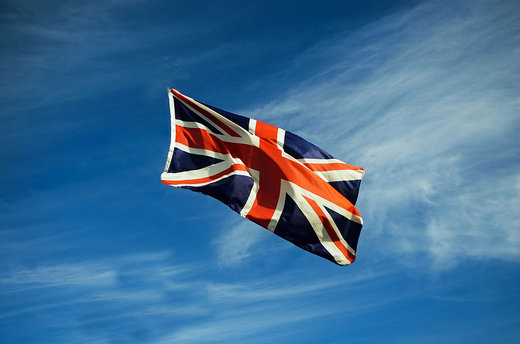
(Jiri Hodan/Wikimedia Commons)
Europe meanwhile faces a “lost decade”, the report’s authors say. Thanks to population decline and sovereign debt pressures Western European construction output will grow by only around 1% per year to 2025.
Growth in the UK will be twice as fast, thanks to a housing shortage and an infrastructure modernising drive, but 2% per annum growth is cold comfort for politicians desperately anxious to boost employment.
So what’s the plan?
The strategy’s authors blame the UK’s poor construction export figures on the fact that, in their words, “very few of our prime companies lead on overseas projects”.
Notwithstanding high-profile wins, such as Mace and EC Harris, project managing Saudi Arabia’s Kingdom Tower, the lion’s share of international bread and butter is being gobbled up by other countries.
The UK has only three firms in ENR’s Top 250 International Contractors list for 2013 (Balfour Beatty, Petrofac and Amec), compared, for instance, to South Korea’s 15 and Turkey’s 38.
In design, Britain does better according to ENR’s calculations, with 10 UK firms on its roster of top 225 international designers (Amec, Arup, Mott MacDonald and Atkins lead the charge) – although this pales in comparison to the profile enjoyed by China, with 32 firms on the list, and the US, with 84.
The new strategy therefore aims to get more British companies overseas.
“Taking steps to enable UK firms to secure the lead role more often,” the authors write, “will enable us to make the most of opportunities in the high growth global construction markets.”
They believe that the spoils of overseas work would be shared at home. They write: “From a lead role, there would be considerable potential to bring in UK-based supply chains, thereby multiplying the potential dividend to the UK.”
To make it happen the government’s exports promoter, UK Trade & Investment (UKTI), will “explore the appetite for a trade ‘grouping’ of UK based contractors”.
UKTI will also “explore the potential” for “an entity to support overseas trade in construction”.
These rather vague actions are to start now, in Autumn 2013, and in Winter 2013/14, UKTI will develop marketing materials “to better promote UK comparative advantage around whole life cost, sustainable construction and BIM”.
In the meantime, the UK’s Construction Products Association (CPA) has received funding for a two-year programme to help non-exporting manufacturers get their products overseas. The CPA says it has helped 200 companies do this in the last three years.
Response
Industry reaction to the strategy in the UK has been muted, but one prominent academic dismissed it outright as vague, and a recipe for “collective inaction”.
Writing in Construction Research & Innovation, Professor Stuart Green, head of construction management and engineering at the University of Reading and author of Making Sense of Construction Improvement, said there was little evidence that companies winning work overseas would boost the fortunes of people at home.
“The overall need seems to be to spin a story of construction market growth and, in the absence of actual growth at home, the fuzzy notion of growth abroad will have to do,” he wrote.
“In truth, construction consultancy firms have been global for years, and their profits and dividends are distributed with scant regard for the needs of UK Plc. There is little reason to think this is going to change.”
Construction economist Brian Green, author of the blog Brickonomics, also questioned the effectiveness of the strategy.
“It would be absurd,” he said, “for a high-wage economy such as ours to expect to have a good export record in heavy and relatively low-cost building materials. Even for high-value products it may be better to manufacture them abroad while keeping the intellectual property in the UK.”
“We need only look to Dyson’s decision to move production to Malaysia to see an illustration of that phenomenon,” he said, adding: “If we are to have any real impact on exporting it must surely be at the very innovative high-end. That suggests to me we need a much closer relationship between research funding, the manufacturers and the wider construction industry.”