Researchers in the US are 3D printing parts of an excavator to probe the possibilities of the technology in manufacturing.
The team at Oak Ridge National Laboratory (ORNL) in Tennessee will use “additive manufacturing” to print the excavator’s cab (pictured), the “stick” (its hydraulically articulated arm) and a heat exchanger.
ORNL believes that increasing the size and speed of metal-based 3D printing techniques using low-cost alloys like steel and aluminium could create new industrial applications.
Additive manufacturing can be used to print components on demand, which could potentially eliminate the need for mass storage, organization and transportation– Lonnie Love, Project leader
The stick will be fabricated with the so-called “Wolf System”, a machine that uses a freeform technique in printing big metal components, while the heat exchanger will be printed on a Concept Laser machine that produces metal parts through a powder-bed-based laser melting process.
The cab was designed by a student engineering team from University of Illinois at Urbana-Champaign, and printed using carbon fibre-reinforced ABS plastic.
During the project the team will look to improve material performance and printability and validate models for reducing residual stress and distortion.
Project leader Lonnie Love said he expects the excavator to be printed, assembled and ready to be unveiled in nine months, according to an ORNL media notice, though parts will be on display in Las Vegas in March.
“The beauty of a project of this size and scope is that it brings together many intelligent people to work on a number of challenges while accomplishing a common goal,” said Love, adding: “We’re … exposing [the next generation of engineers] to the possibilities that additive manufacturing is affording industry that can help companies from so many different areas whether it’s automotive, construction or other applications yet to be discovered.”
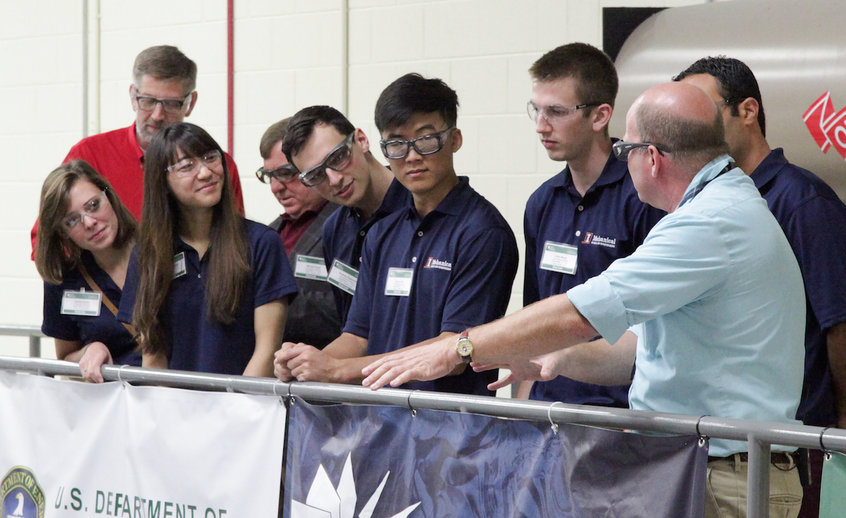
ORNL’s Lonnie Love, on right, with a student engineering team from the University of Illinois at Urbana-Champaign (ORNL)
While 3D printing excavators may not become common practice among manufacturers, Love said using additive manufacturing to print low-volume, high-complexity components could benefit the construction industry by reducing production time and cost.
“Additive manufacturing can be used to print components on demand, which could potentially eliminate the need for mass storage, organization and transportation,” Love said.
The project was funded by the US Department of Energy’s Advanced Manufacturing Office.
Photograph: The cab was designed by a University of Illinois at Urbana-Champaign student engineering team, and printed using carbon fibre-reinforced ABS plastic (ORNL)
Further reading:
Comments
Comments are closed.
Has there been a whole life analysis and the environmental impact carried out