A team from the US Marine Corps’ Systems Command (MCSC) and Naval Construction Battalion has used the world’s largest concrete 3D printer to create a barracks hut.
Located at the US Army Engineer Research and Development Center in Champaign, Illinois, the 47 sq m structure took 40 hours to print, while marines monitored progress and continually filled the printer with concrete.
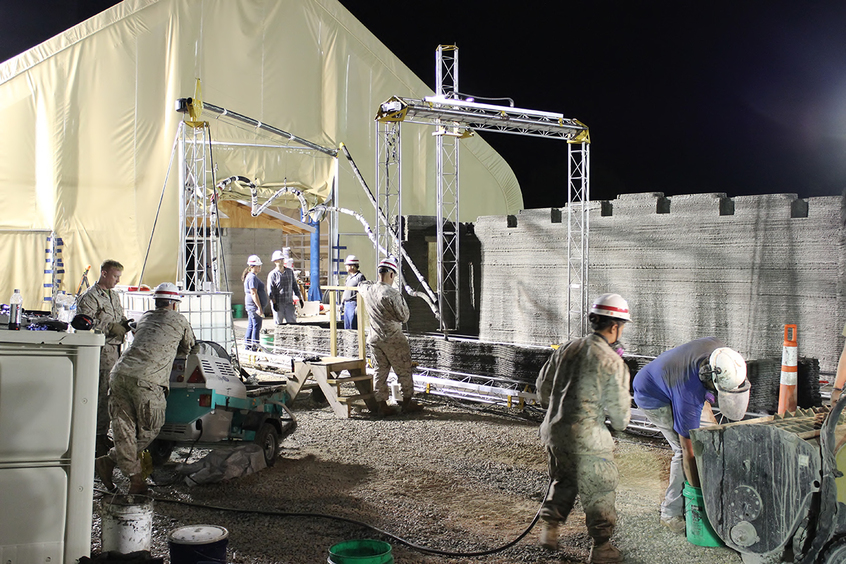
Building a wood barracks hut would normally take 10 marines five days.
Matthew Friedell, MCSC project officer, said the experiment was the first of its kind. “People have printed buildings and large structures, but they haven’t done it onsite and all at once. This is the first onsite continuous concrete print.
“In active or simulated combat environments, we don’t want marines out there swinging hammers and holding plywood up,” he said.
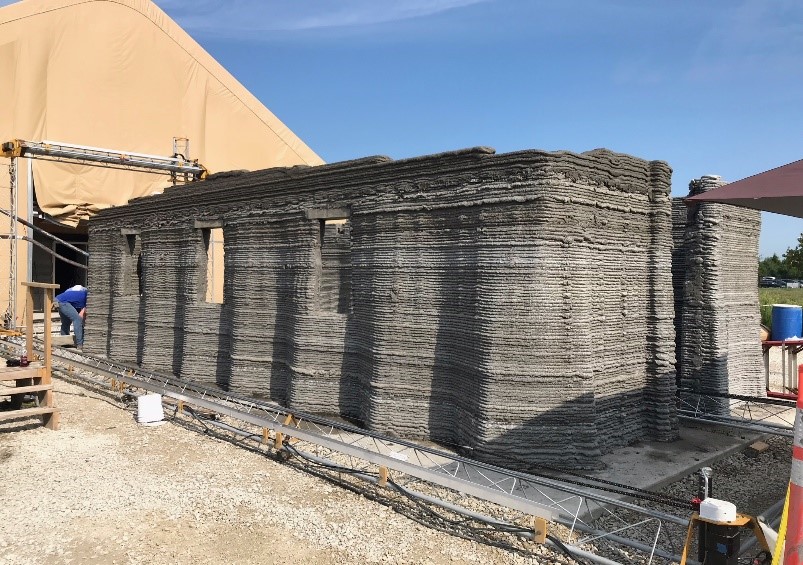
The Marine Corps also plans to use concrete printers in humanitarian aid and disaster relief missions. In many locations, cement is easier to acquire than wood, and marines could print houses, schools and community buildings to replace those destroyed.
Images courtesy of the MCSC
Comments
Comments are closed.
Whilst I can see some benefits in 3D printing they still need to transport the “printer” and feed the machine with concrete. I question, however, whether this is faster than erecting a prefabricated structure. I also question the thermal efficiency of the structure in extreme climates. As for the appearance I guess that this is the least of their worries but it certainly won’t win any design prizes.
How Hadrian could have made the Wall in the UK more quickly if he’d had this…But there is much to be said for on-hands training – it is schematic for other initiatives that require how to use tools: I’ve seen many a so-called wild-life conservationist and university graduate in proposed countryside and other outdoor careers unable to use a spade or ax or even a screwdriver properly.
Remember those recent incidents involving the US Navy, where the basics of seamanship were found to be missing. The present Marines are adept at practical skills, but what happens if basic tools stuff isn’t handed on?
Still, this is obviously a most useful innovation; quite incredible.
But will it need another 100 hours and many kg or materials and craftsmen to smooth out the bumps so you can attach stuff to it? Lots of thermal mass, no windows. Where is the thermal insulation? Where is the moisture permeability? Mechanical ventilation essential then.
The timber huts could be carbon negative this one is carbon positive. Cement production accounts for 8-10% of manmade CO2. Did they use low carbon cement? Did they use recycled aggregate?