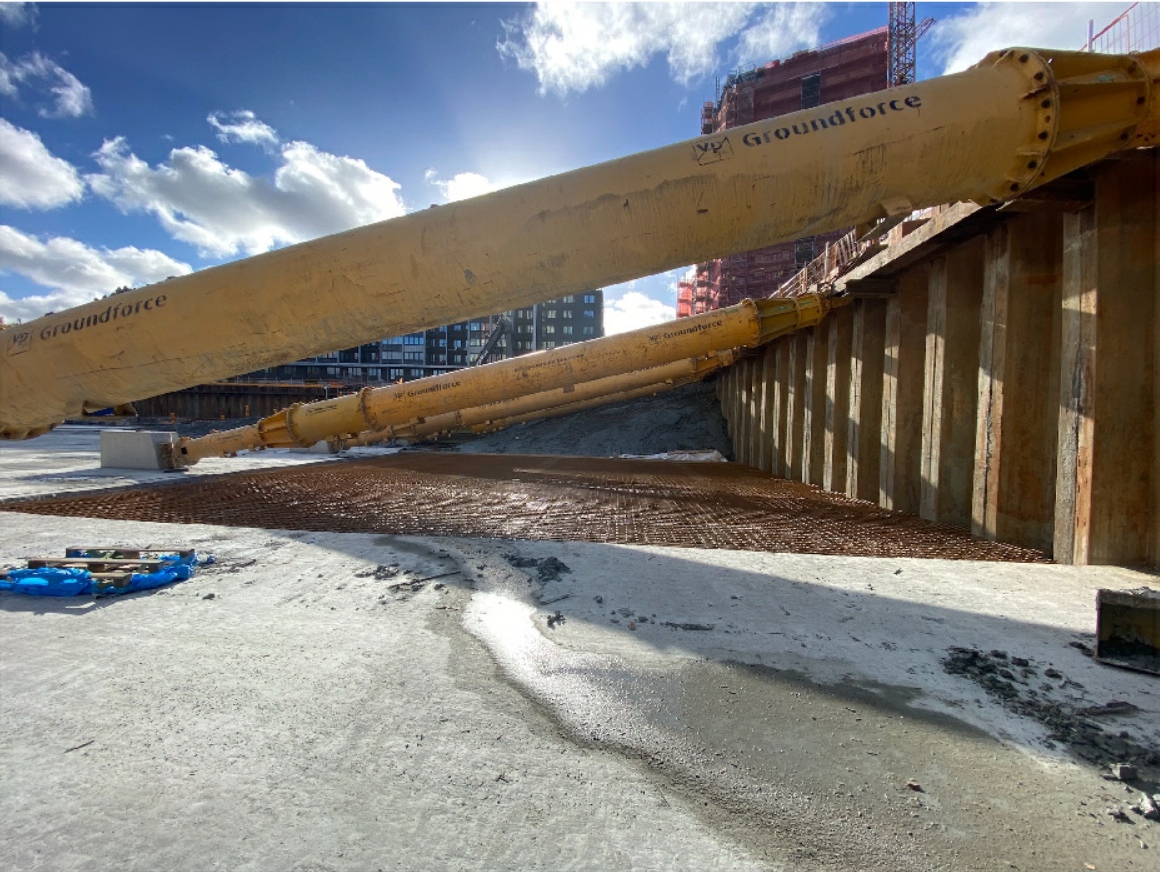
The Swedish city of Gothenburg is getting its first skyscraper, the 245m Karlatornet tower designed by US architect Skidmore Owens & Merrill, set to be the centrepiece of a new mixed-use district called Karlastaden.
The tower was on its way to topping out last year thanks to an innovative shoring technique that protected the integrity its six-metre-deep excavation in Gothenburg’s soil, which is challenging to build on owing to its deep clay deposits.
Instead of opting for a bespoke, fabricated-steel shoring structure, Karlatornet’s developer and builder Serneke Group opted for props that could be moved around to hold up the walls of the excavation while permanent retaining walls were built.
Shoring and bridge specialist Groundforce supplied 12 of its heavy-duty MP250 modular hydraulic props to keep the excavation, measuring 90m by 90m in area, from falling in on itself.
Big, wide hole
Normally the Groundforce props are used to brace one side of the excavation against the opposite side – bearing against a concrete capping beam or one of Groundforce’s modular steel waling beams.
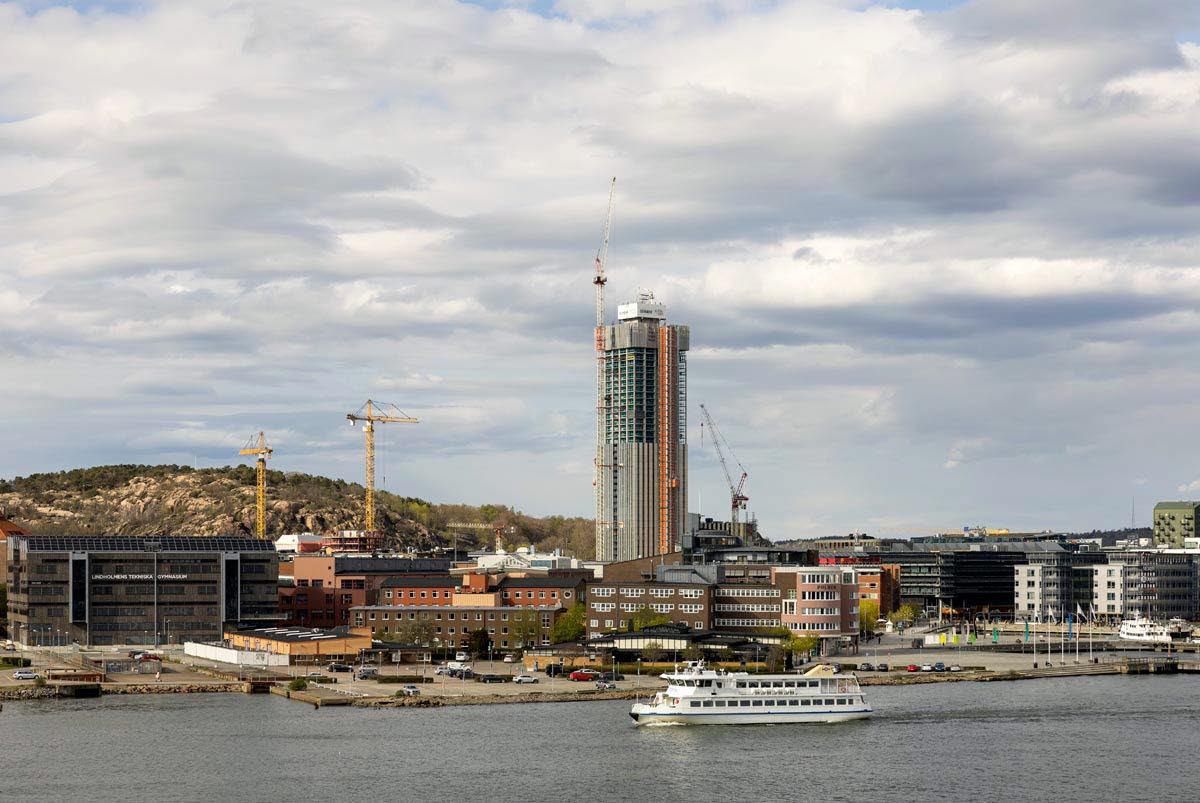
But this approach doesn’t work with extra-wide holes. Excavations wider than 30m can’t be propped without the props themselves being propped up in the middle; 90m spans are quite impractical.
So, on the Karlatornet project, “raking props” were used, where the prop rests against a solid “thrust block”, usually a large in-situ cast concrete block embedded in the ground.
To support the 6m-deep excavation, Groundforce supplied 250-tonne capacity MP250 props ranging in lengths from 17.5m to 20.5m.
Rationing support
The size of the excavation meant it was impractical to hire in enough props to support the full perimeter of the excavation all at the same time.
So, the team decided to build the basement in phases, propping each excavation wall until its corresponding floor slab and retaining wall were done.
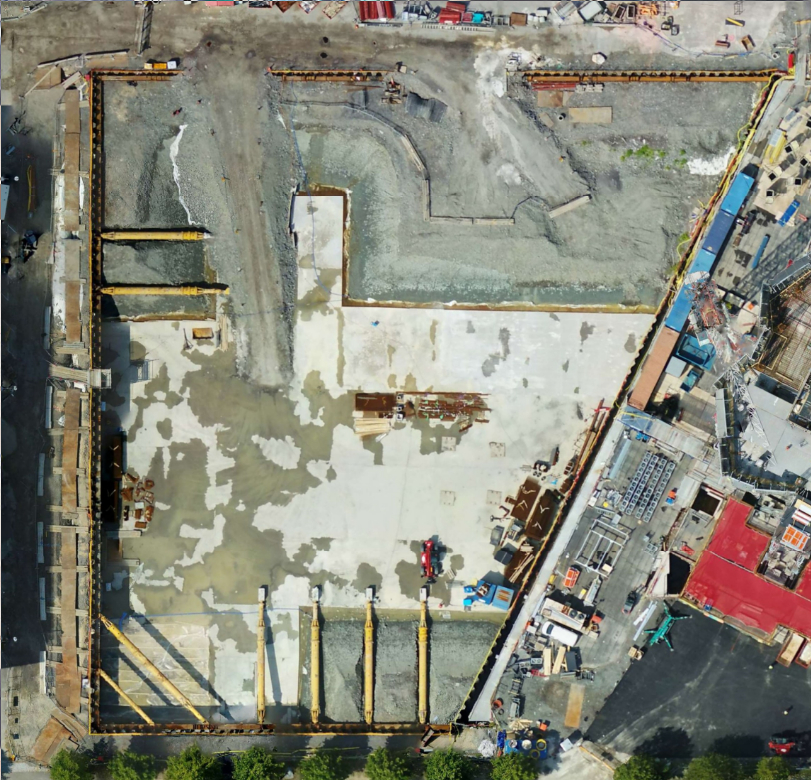
The props are then leap-frogged from one section to the next as construction progresses.
“One of the reasons our modular system was chosen is that the components are very quick and easy to install and disassemble,” said Groundforce European sales manager Sam Oldroyd.
“It would have been much slower and more complicated if bespoke fabricated steelwork had been used,” he adds.
Thicker extension tubes
Groundforce proposed the use of its MP250 props equipped with 1,016mm-diameter “Eurotube” extensions.
The standard extension tube for the MP250 is 600mm in diameter, but at spans ranging from 17m to more than 20m, these would have been too slender and subject to deflection.

Developer Serneke could have specified Groundforce’s “Super Tube”, which has a diameter of 1,220mm, but those extra 204mm would have been a disadvantage in this case, what with the props being delivered from the company’s main European depot in Hanover, Germany.
Sam Oldroyd explained: “The advantage is that we can get four Eurotubes on a single wagon, whereas we can only get two of the larger Super Tubes on a wagon.”
That allowed the team to cut the transport requirement, reducing cost and emissions.
Serneke’s project manager Zimon Gustafsson said the props were a wise choice for the Karlatornet project. “This is my third project in Gothenburg and we’ve used Groundforce equipment on all three,” he said.
“Hopefully it will save us both time and money – it’s quite obvious to me that this system is cheaper in the long run, especially as steel prices have gone up so much recently. There really weren’t many other alternatives.”