Builders could not use cranes to erect the roof of Hong Kong’s new Passenger Clearance Building because it is just 2m below the allowable ceiling that guards flight paths into the adjacent Hong Kong International Airport. So, Robert Bird Group devised a pioneering method of slotting 81 prefabricated segments horizontally on rails into place to get around height and other serious space constraints.
Robert Bird Group (RBG) was appointed during the tender phase by Leighton Asia with its joint venture partner, Chun Wo Development Holdings, as the specialist construction engineering consultant for the Hong Kong Boundary Crossing Facilities – Passenger Clearance Building (PCB, pictured), designed by Aedas International and Rogers Stirk Harbour & Partners.
The Highways Department of the Hong Kong Special Administration Region Government is the PCB project promoter.
RBG was required to design and develop in close consultation with the Leighton-Chun Wo Joint Venture the construction methodology and erection sequence (CMES) for the construction of the building’s iconic roof element.
The PCB is a building with a total floor area of over 90,000 sq m, located on a man-made island adjacent to the Hong Kong International Airport. It is the new border crossing point for travellers between Hong Kong, Macao and Zhuhai, China, and serves as an immigration gateway for vehicles and passengers entering and leaving Hong Kong.
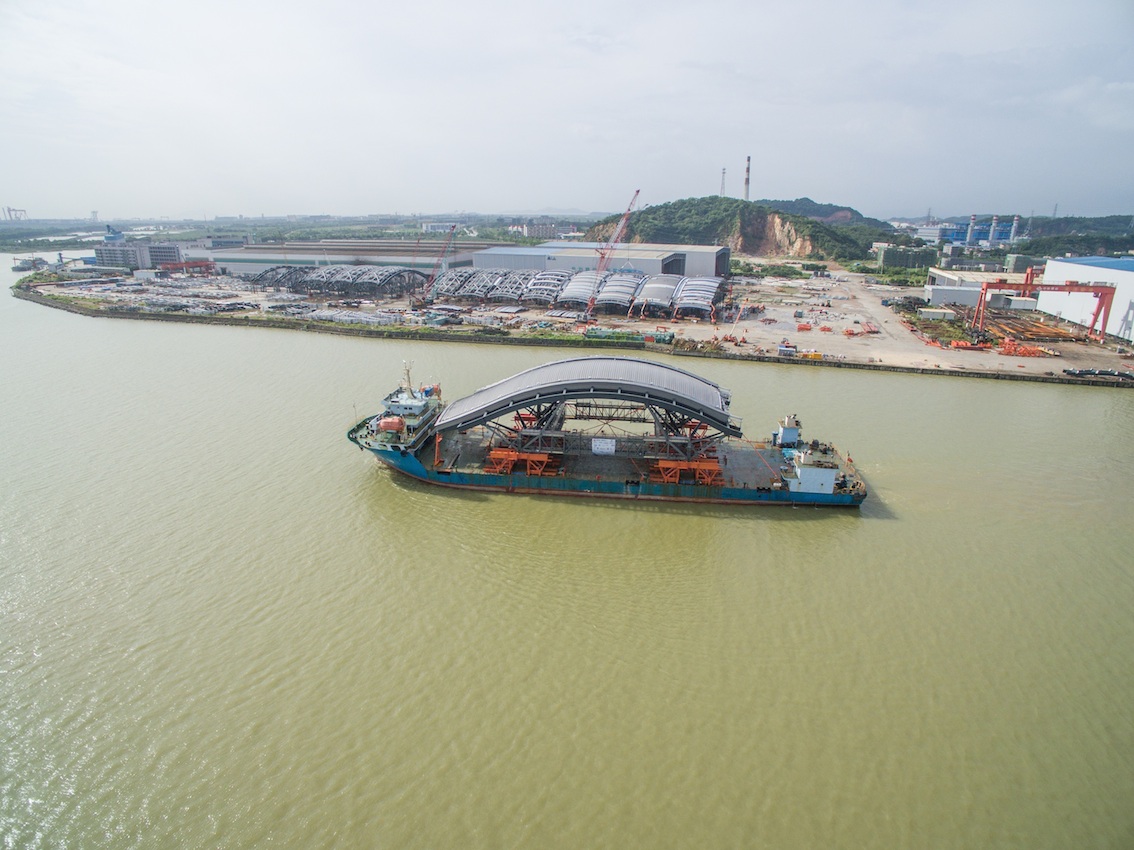
Roads were unavailable, so 81 custom-prefabricated roof segments, with temporary transportation frame attached, were barged in sequence to the PCB site’s purpose-built jetty
The PCB includes a 300m long by 200m wide wave form iconic roof; the roof structure is composed of structural steelwork with the building zoned into a series of structured bays, supported by steel cast nodes with prop arms that support the major structural steel framing elements of the roof.
The roof cladding is a fully integrated cassette system overlaid with a preinstalled standing seam roof sheeting. The facades are all double-glazed, supported by a series of bow-string trusses that span 16m vertically between the floor and the roof.
RBG was tasked to investigate the permanent works design and develop an innovative construction solution that could address the unique constraints associated with construction of the PCB.
The building is located directly beneath the flight path and the emergency flight descent zone into the airport. One of the major constraints to construction was the air height restrictions imposed by the Civil Aviation Department of Hong Kong.
This limited the height to which the building and construction equipment could rise. The roof being just 2m under the air height restriction meant that traditional methods of construction from above using cranes could not be used for the roof construction.
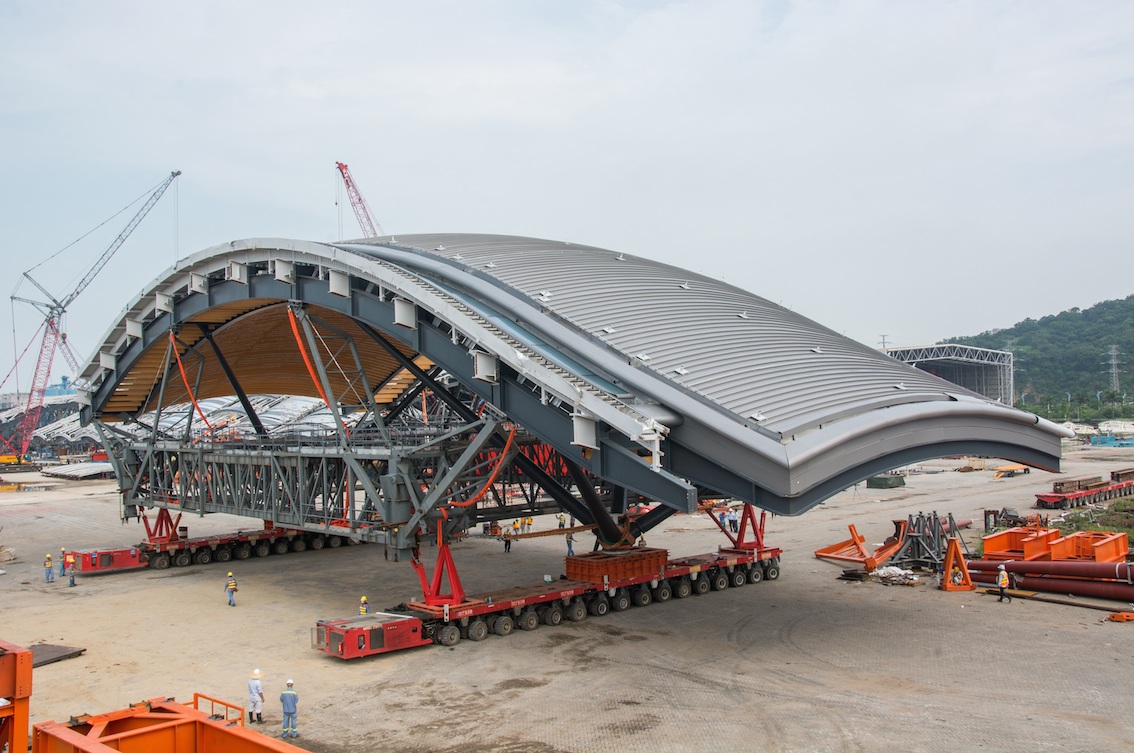
Self-propelled modular transporters (SPMTs) were used to get the roof segments off the barges and to location
A further constraint was that the PCB would occupy one small part of the reclaimed 130ha island at just over 6ha and be surrounded by the construction of roads, bridges, gates, and ancillary buildings that connect the island to the airport. These were all being constructed at the same time which would have meant sharing the temporary access roads with other contractors leading to serious congestion.
If the roof had been built in the traditional method there would have been the need for large areas for lay-down and on-site preassembly which was not possible because of the limitations of the available site area.
To demonstrate to the Leighton-Chun Wo Joint Venture and the Highways Department the proposed PCB roof construction methodology and erection sequence at the tender stage, RBG utilised Virtual Design and Construction (VDC) to visualise the construction methodology. Still images were produced from the Revit model for the permanent design elements and temporary works which were then transferred into the 3DS Max software for processing.
In the initial stages of the post award design phase the Leighton-Chun Wo Joint Venture finalised the model of the permanent and temporary works in Revit and produced a BIM model incorporating the input from all subcontractors including RBG’s temporary works, the roof permanent works from the steel contractor as well as the transport frames all done using BIM and Navisworks.
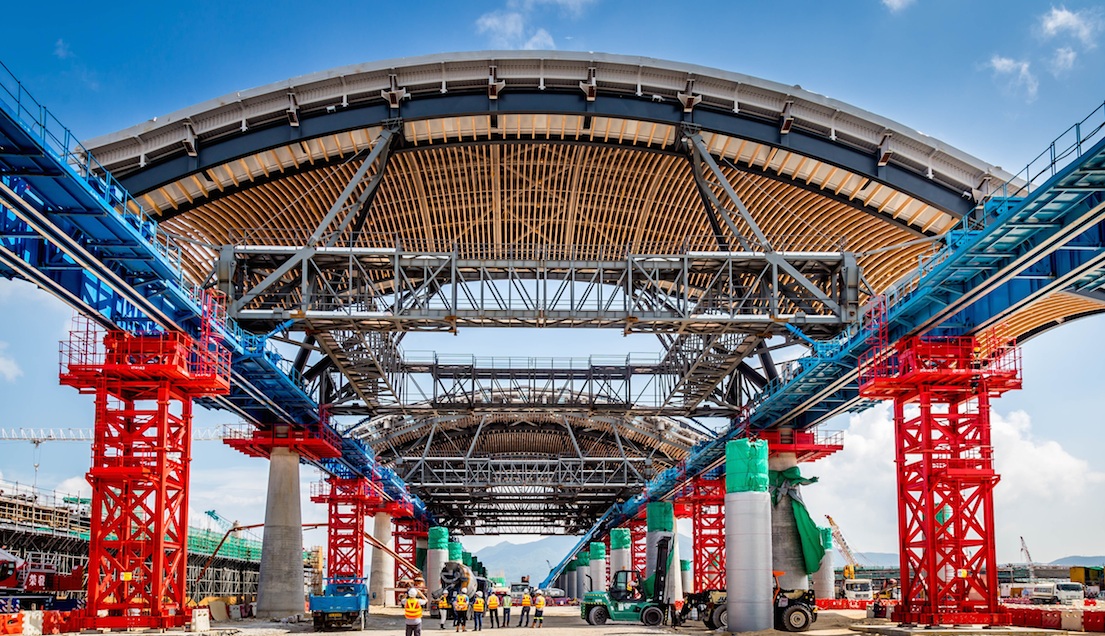
Heavy lift contractor VSL lifted the segments in sequence using their purpose-built heavy lift hydraulic platform
The construction methodology adopted by the Leighton-Chun Wo Joint Venture and RBG was to use off-site prefabrication and preassembly with the roof built in segments as part of a full-scale outdoor roof assembly line in Zhongshan, China.
The roof segments would then be horizontally launched into their final positions above the constructed concrete structure.
The roof was broken down into 81 segments: 45 primary and intermediate roof segments and 36 infill segments. The segments were preassembled complete with structural steel elements, roof cassette cladding, architectural builders’ works and finishes (ABWF) and MEP. They were then transported by barge to the Hong Kong site.
Due to the congested waterways around the island, including the Macao ferry terminal connecting the island to the mainland, there was only one possible barging point that could be used.
A temporary jetty was built on the reclaimed island to receive each barge carrying a roof segment mounted on its temporary transportation frame. Naval architects working with RBG determined the forces that the barges would be subjected to in crossing the Pearl River delta, including the impact of wind and waves, which was then used by RBG for the design of the transportation frames and barging temporary works.
Self-propelled modular transporters (SPMTs) were used to get the roof segments on and off the barges. The SPMTs were also used to navigate the segments around the project site including the offsite assembly yard.
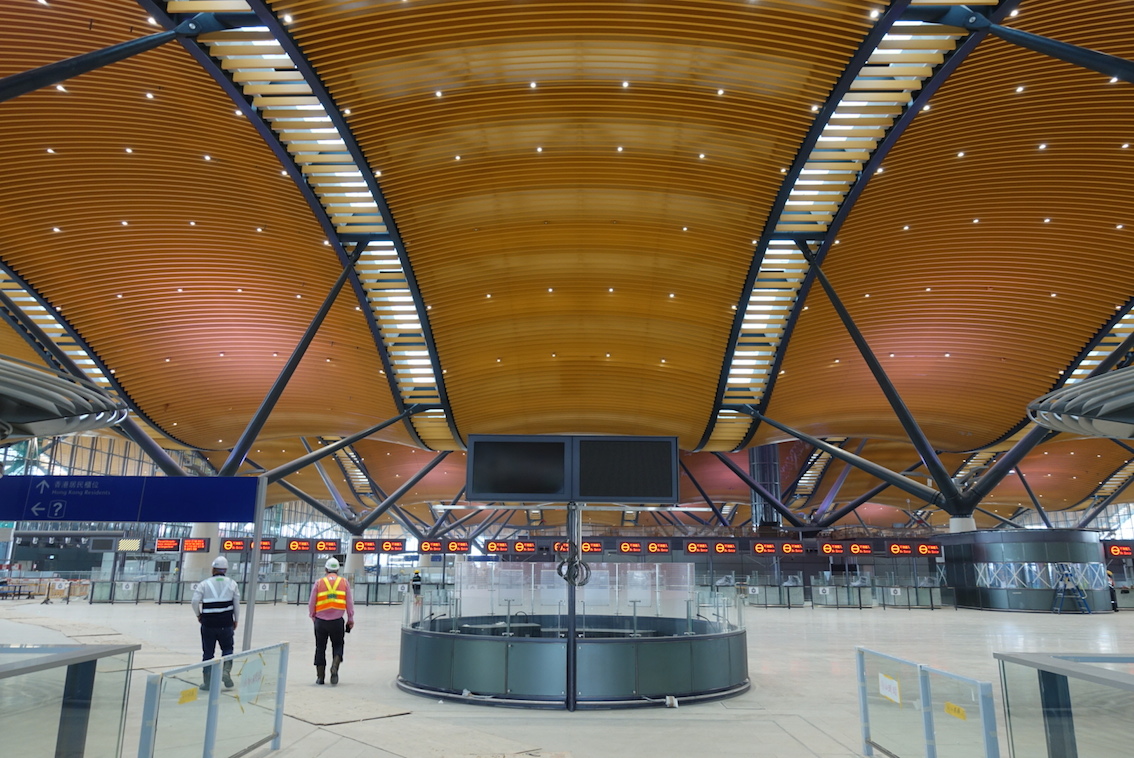
Roof segments arrived on site complete with structural steel elements, roof cassette cladding, architectural builders’ works and finishes and MEP
Heavy lift contractor VSL lifted the segments in sequence using their purpose-built heavy lift hydraulic platform located on the road outside the building. The segments were lifted with the use of strand jacks to a height where they were aligned with the temporary elevated rails supported by the reinforced concrete columns and temporary towers, horizontally launched along the rails into position and then connected to concrete mega columns and the adjacent roof segments that were already in place.
In conclusion, the horizontal launch erection sequence solution designed by RBG and developed with the Leighton-Chun Wo Joint Venture proved to be the right approach for the project, with the process being extremely time efficient so that the entire roof was erected in just over nine months from delivery of the first roof segment.
Due to the success of the modularisation, off site preassembly and horizontal launch erection process, it has now become part of the CMES for the Third Runway Concourse building that is to be constructed for airport.
RBG expects that in future design modularisation, off site preassembly and horizontal launch CMES will become the game changer for the delivery of large and public assembly buildings at locations like airports and other constrained sites around the world.
Contact Robert Bird Group for more information.Â
Images courtesy of Robert Bird Group