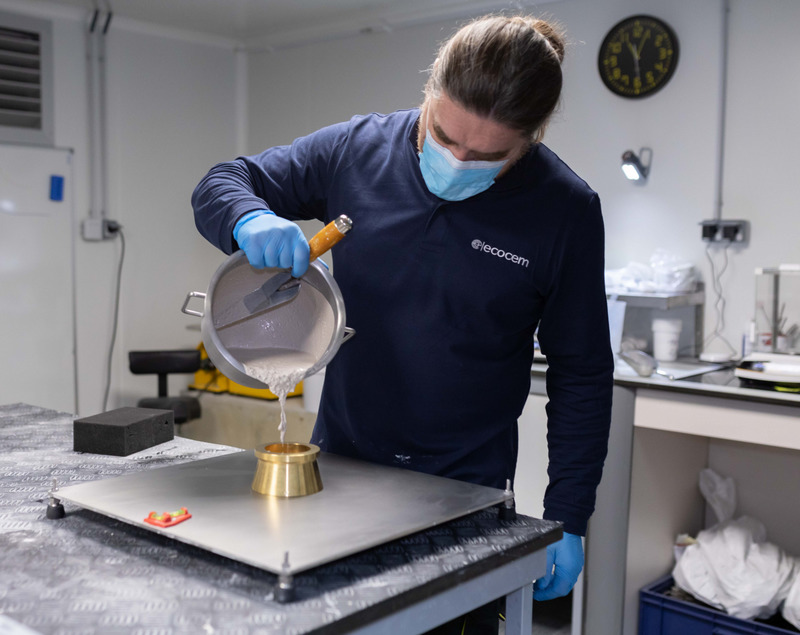
The global construction industry stands at a crossroads. As outlined by the World Bank’s International Finance Corporation, if trends persist, global carbon emissions from construction are projected to increase 13% by 2035. Considering that the industry is responsible for around 40% of global energy and industrial-related emissions, the need for action becomes even more pronounced.
The mandate is clear: the construction sector must undergo a substantial transformation to curb its carbon footprint and chart a course toward a sustainable future.
To that end, industry players – both big and small – must commit to accomplishing three goals. Firstly, to minimise the carbon emitted during the production of building materials, especially steel and cement. Secondly, to adopt circular economy principles to curb waste and support sustainable resource consumption. Lastly, to move away from the industry’s reliance on fossil fuels and embrace eco-friendly alternatives.
Although attaining these goals will present challenges, making a systematic, industry-wide effort will be essential, not only for fostering a greener future but also for shaping a construction industry that is more efficient, adaptable, and innovative.
Carbon mitigation
The production of building materials results in unavoidable carbon emissions. Producing clinker (the main ingredient in cement) is the most carbon-intensive part of the process. And since cement is necessary for concrete – the world’s second most consumed material behind water – traditional methods of cement and concrete production are an environmental problem.
Portland cement, the most common type, is made by heating powdered limestone in a rotary kiln to create clinker – the component that confers binding properties. This results in the emission of about 535kg of carbon dioxide for every tonne of clinker produced (excluding indirect emissions from the fossil fuel used in the heating process). Think about that: for every tonne of cement created, the process generates over half a tonne of carbon.
Fortunately, the past decade has yielded significant progress in ways of diminishing carbon emissions in the cement production process. The most promising is carbon capture, utilisation and storage (CCUS).
This is a suite of technologies that allow heavy industries such as cement to recapture carbon emissions during their production processes or directly from the air. These emissions can then be stored underground in geological formations, utilised to enhance concrete strength (among other uses), or employed in the production of other goods.
Compared with other decarbonisation methods, CCUS is particularly promising owing to its potential to slash up to 40% of all related emissions in one go. However, most CCUS projects are still operating at a small scale through start-ups.
Major hindrances to mass adoption include the high upfront costs of acquiring and operating CCUS technologies, coupled with the traditional risk averse mindset in the cement industry.
That is changing, though, with the development of more cost-effective CCUS technologies, the availability of government grants, and a growing emphasis on sustainability among major producers.
An example of this trifecta for success is the £2.3m grant from UK Research and Innovation (UKRI) awarded to a consortium led by Carbon Upcycling, a notable carbon capture and utilisation start-up, for the world’s first commercial-scale cement additive plant combining carbon sequestration and industry by-products.
A circular economy
The construction industry generates a lot of waste: about 600 million tonnes a year in the US alone. Of this, 90% comes from demolition, and most of that ends up in landfills.
Simultaneously, the construction industry is grappling with resource shortages and surging demand, resulting in a substantial rise in the costs of traditional building materials such as concrete, sand, and timber.
One solution that could address both the industry’s waste problem and resource shortage is the circular economy.
This model maximises the lifetime value of building materials by keeping them in use for as long as possible. Instead of just tearing down structures, some demolition companies are carefully dismantling them, saving materials for reuse or recycling. By keeping waste to a minimum and recovering materials, the construction industry can tackle resource scarcity, make rare resources more affordable and reduce its carbon footprint. In fact, in a recent report by the McKinsey business consultancy, cement and concrete have the highest carbon abatement potential through circular strategies.
To transition successfully to a circular economy, construction will need to embrace new methodologies. Personnel will have to be trained to dismantle structures in ways that salvage the maximum amount of materials for reuse. New supply chains and infrastructure upgrades will be necessary to bring recycled materials back into the supply chain. True, this is an expensive proposition, at least in the short term. However, once you consider the long-term benefits, a circular economy becomes a sustainable and an economically viable choice.
Investing in new supply chains, infrastructure and staff training can yield returns through increased efficiency. Adopting a circular economy would also serve as a pre-emptive measure against growing scrutiny from governments and regulatory bodies. By getting ahead of the regulators, the construction industry can future-proof itself against impending regulations and penalties.
The clean energy transition
With each passing year, the construction industry faces growing pressure to shift away from fossil fuels. Since nearly 98% of the industry’s energy is derived from diesel, going green is not something that the industry can accomplish overnight. Nevertheless, establishing and pursuing a long-term energy transition is no longer a secondary consideration: it is a necessity.
Take, for instance, the fact that diesel prices have surged 33% in the past year alone. This increase, coupled with persistent disruptions in the supply chain and dwindling inventories, mean continued dependence on diesel is a precarious proposition for the sector. Adding to that, regulatory pressure is building for the industry to reduce its carbon footprint, a significant portion of which stems from its dependence on fossil fuels.
Fortunately, advances in green energy alternatives have been made. Two options that are particularly promising are zero-emission hydrogen fuels and fuels derived from waste. For example, so-called emerald hydrogen, produced through thermal plasma electrolysis, offers strong potential as an environment-friendly fuel source that co-produces only carbon black, a fine powder that can be used as a reinforcing filler in rubber products or as a black pigment in inks and paints, among other things.
At present, alternative fuels are relatively expensive and there has been limited take-up. However, technological advances and increased production are expected to reduce expenses. To make progress, though, increased investment and collaboration with start-ups will be crucial. This goes not just for alternative energy sources, but also for the production of sustainable building materials and the promotion of the circular economy. Start-ups have a big part to play in all three endeavours, since they offer the innovation, the agility and the drive to create a sustainability revolution in the construction industry.
HiiROC is one example of a Cleantech start-up with a low-cost, zero-emission hydrogen solution that can be applied to high-emitting sectors such as construction. In fact, Cemex, the company I work for, is planning the large-scale deployment of HiiROC’s thermal plasma technology to reduce its consumption of fossil fuels and decarbonise its cement making operations.
What these start-ups do not have, though, are the resources, industry knowledge and global networks they need to make those ambitions a reality. That is where partnerships with larger companies come into play. By forming collaborative alliances, start-ups can leverage the expertise and established networks of larger companies, and larger companies can gain access to innovative technologies and fresh perspectives. These mutually beneficial partnerships contribute to a more robust and efficient development process, with benefits that redound to the larger good.
Final thoughts
The construction industry’s response to the carbon emissions crisis is not just a matter of compliance with environmental regulations; it is a strategic imperative for long-term viability. The path ahead demands a fusion of innovation, collaboration and a commitment to creating an industry that not only meets the needs of today but also safeguards the planet for future generations.
- Alfredo Carrato is an investment and open innovation adviser at Cemex Ventures, Cemex’s corporate venture capital and open innovation unit
Further reading: